Blow Moulding
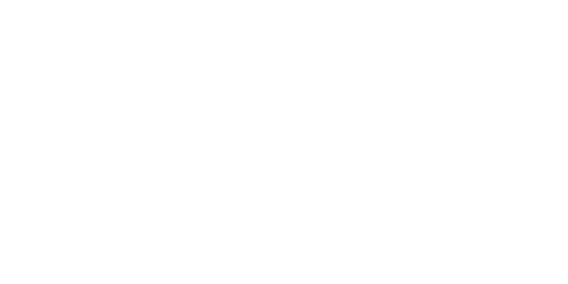
Whether you are looking to produce PET bottles or cosmetic containers, Tritan or PP or PE bottles, Aoki Technical Labs from Japan have a suitable solution for you.
Aoki are the world leader in 3-stage Injection-stretch-blow moulding machines & tooling. In simple terms no other supplier of ISB machines can produce bottles at a lower cost per bottle.
Aoki pride themselves on providing blow moulding technologies that are energy efficient and help the environment. PET bottles are an excellent example of this. PET is the most commonly recycled plastic and bottles produced with Aoki injection-stretch-blow machines & tooling provide users the lowest possible carbon footprint.
We also offer a full range of ancillary equipment suitable for blow moulding operations, including material handling, chillers, desiccant dryers, and automation solutions for downstream.
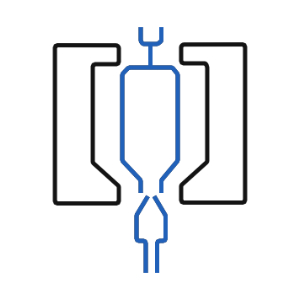
A step-by-step description of the blow molding process:
- Extrusion: The process starts with the extrusion of a thermoplastic material, usually in the form of pellets or granules, into a molten state. The plastic resin is melted and compressed in an extruder, which consists of a heated barrel and a rotating screw. The rotating screw pushes the molten plastic forward, melting it completely and creating a uniform melt.
- Parison Formation: Once the plastic material is molten and homogenous, it is extruded through a die head to form a tube-like shape called a parison. The parison is a hollow tube with a cross-sectional shape that corresponds to the final shape of the product. The size and length of the parison are controlled by adjusting the extrusion speed and the die shape.
- Mould Closing: The parison is transferred to a mould, which consists of two halves. The mould halves close around the parison, and a small amount of compressed air is introduced through the blow pin or mandrel. The compressed air inflates the parison, forcing it to conform to the shape of the mould cavity.
- Blow and Cooling: As the parison is inflated, the molten plastic is pressed against the inner walls of the mould, taking its shape and solidifying. The mould is designed with cooling channels to facilitate rapid cooling of the plastic. The cooling time varies depending on the material and the size and thickness of the product. Once the plastic has cooled and solidified, the mould is opened.
- Part Ejection: The mould halves separate, and the newly formed plastic part, now in its final shape, is ejected from the mould. The excess plastic, called flash, may be present at the parting line of the mould. This excess material is trimmed off and recycled for future use.
- Repeat: The process is repeated to produce multiple parts in a continuous cycle. The cycle time varies depending on factors such as the size of the part, material properties, and cooling time required.
Get Started