Extruding
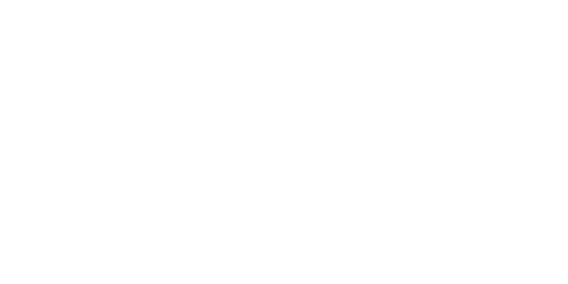
For over 50 years, Tasman Machinery has been a supplier to the extrusion industry in Australia and New Zealand.
Tasman Machinery is proud to partner with several famous extrusion industry brands Bausano & Figli is known the world over for producing excellent twin & single screw extruders for pipe, profile, and compounding industry. With all key components manufactured in house Bausano’s engineering is second-to-none.
The famous yellow of Labtech Engineering is known the world over. Extrusion lines for research & development & pilot lines. 16mm -36mm twin screw extrusion for Compounding; Mono to 11 layer blown & cast film lines, medical tube production, profiles & sheet, 3DP filament, Labtech Engineering is famous the world over.
Gear pumps, screen changers and under water pelletizers from Nordson BKG, and extrusion screws and barrels from Xaloy.
Material handling and drying & blending systems from Plastic System, or pressure transducers and instrumentation from Gefran.
Tool-Temp temperature control units have been delivering accurate temperature control to sheet extruders and compounders for over 50 years. Whether using water for temps to 95Deg°C. or oil units for 200+°C, or pressurized water units to 160°C Tool Temp offer a full range of solutions. Swiss built quality is assured.
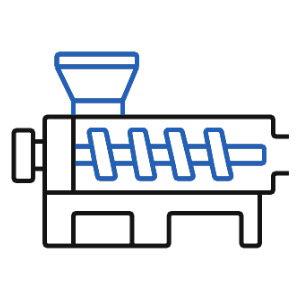
A step-by-step description of the extrusion process:
-
Material Preparation: The chosen thermoplastic material is typically fed into the extruder in the form of small pellets or granules. The material may be a single polymer or a blend of different polymers, depending on the desired properties of the final product.
-
Hopper and Feeding: The material is loaded into a hopper, which acts as a reservoir for the raw material. From the hopper, the material is gravity-fed or mechanically transported into the feeding section of the extruder.
-
Heating and Melting: In the extruder, the material is conveyed forward by a rotating screw within a heated barrel. The screw conveys the material towards the die while subjecting it to heat and pressure. The heat causes the material to melt, converting it into a molten or viscous state.
-
Metering and Mixing: Within the extruder, additional elements such as feeders, mixers, or screws with specialized designs can be incorporated to ensure uniform blending of additives, colorants, or reinforcing agents with the base polymer. This step is crucial for achieving the desired properties and characteristics of the final product.
-
Die and Shaping: As the molten material reaches the end of the extruder barrel, it passes through a specially designed opening called a die. The die determines the shape and dimensions of the extruded profile. The molten material is forced through the die, which imparts the desired cross-sectional shape, such as a tube, sheet, rod, or profile.
-
Cooling and Sizing: Once the material exits the die, it is rapidly cooled to solidify and retain its shape. Cooling methods may involve water baths, air cooling, or other cooling techniques, depending on the material and the desired properties. In some cases, sizing or calibration processes are employed to ensure the extruded product meets specific dimensional tolerances.
-
Cutting and Winding: After the extruded material has solidified, it is cut into the desired lengths or wound onto spools or reels for further processing or use. The cutting method may vary based on the type of extruded product, with options such as saw cutting, guillotine cutting, or automated cutting systems.
-
Post-processing: Depending on the intended application, the extruded product may undergo additional post-processing steps such as surface treatment, coating, printing, or machining to achieve the desired final form or appearance.
Get Started